Folldal Recycling - Drying PE film
Environmentally Friendly and Energy-Saving Drying of PE Film
Folldal Gjenvinning saves between 100 and 150 kW/h per production line by pre-drying washed plastic film in a RUNI Screw Compactor.
Folldal Gjenvinning, a division of Norfolier Norge AS, is one of Scandinavia’s largest recyclers of plastic film. With its latest production expansion, the division’s annual capacity has reached 15,000 tons of PE granulate reclaimed from used plastic bags and packaging film from all over Norway. For each kilo of recycled granulate produced, two kilos of crude oil and four kilos of CO2 emissions are saved compared to production of new plastic.
Environmentally conscious business
Since the start of 1994, it has been imperative for Folldal to meet or exceed the government’s environmental requirements at all times.
“We do our best continuously to improve our environmental work. As a recycling business, we have a special obligation to protect the environment as much as we can so we can take our share of responsibility for the environment,” says Frode Brendryen, Production Manager at Folldal.
Production is very environmentally friendly. No chemicals are used to wash and clean the plastic waste – only clean water – just as the process itself does not emit toxins into the water or air. But Folldal also thinks of the environment in the production lines and their energy consumption which is an important reason why drying is carried out using RUNI SK370 Screw Compactors.
Saves up to 150 kW/h per machine
“We use RUNI in our washing systems on all three – soon four – production lines. It was a solution we came to very early, developed in an excellent partnership with RUNI. The Screw Compactor is used for pre-drying prior to the tumble dryer. The advantage is that we can press out a lot more water before drying and achieve a very low residual humidity of between 10 and 15 % so we don’t need large energy-hungry drying machines. In this way, I would estimate that we save between 100 and 150 kW / h per line and at the same time we avoid heavier machinery,” says Frode Brendryen.
De-watering of reject
In addition to the machines on the production lines, Folldal also uses a RUNI SK240 for the compacting and dewatering of reject. The water from all the machines is reused in the washing process.
Stable despite great wear and tear
“Even though production means great wear and tear on the machines, they are very stable and we are extremely satisfied with their performance. Our lines run 24/7 and that means approx. 7,300 operating hours per annum. Service is also impeccable. Even when we experience unusual breakdowns, we receive spare parts extremely quickly,” says Frode Brendryen.
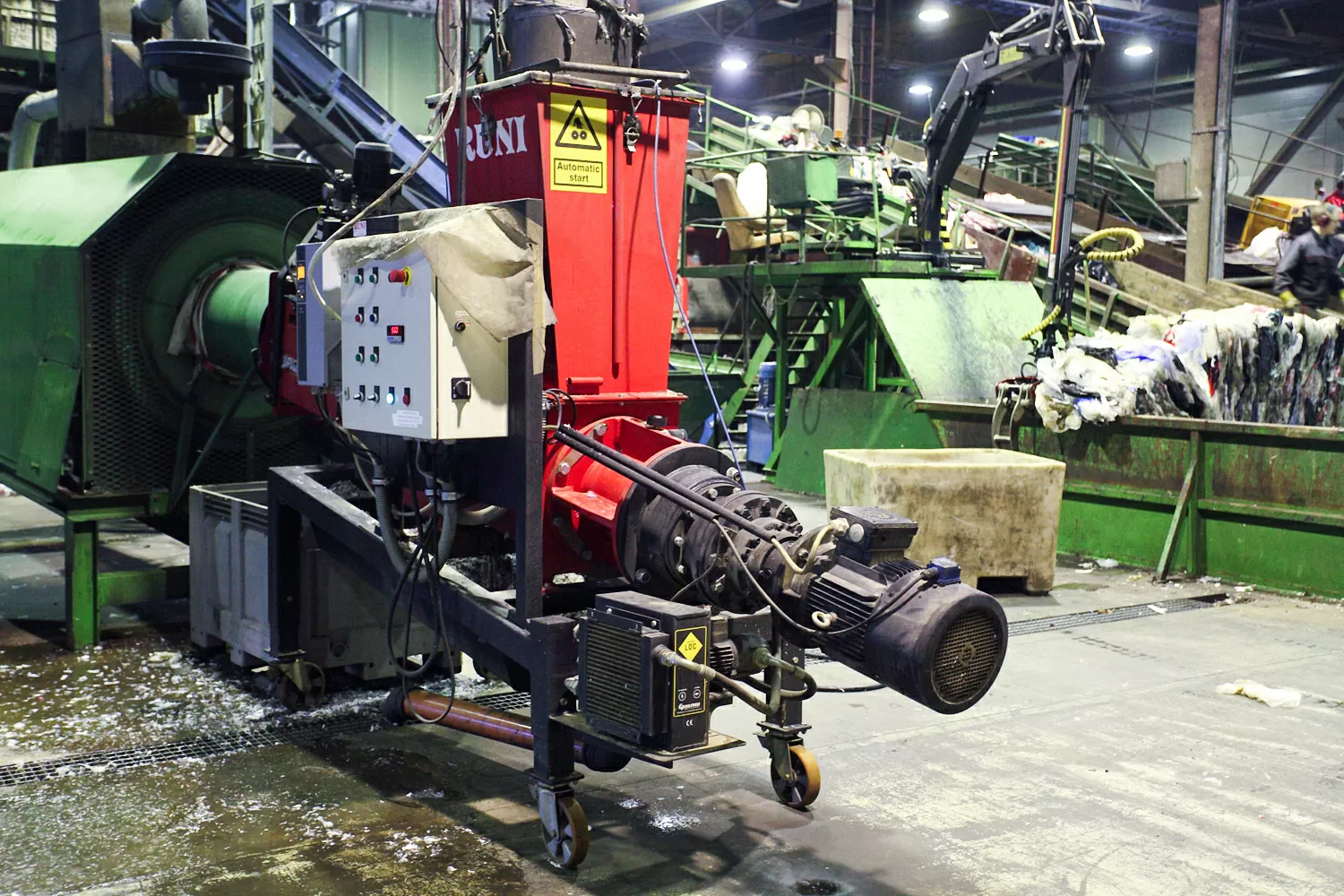